TECHNOLOGIES FOR EXPLORATION TO REFINING PROCESS
Industrial automation in the oil and gas industry utilizes advanced technologies to enhance exploration, production, and refining processes. By incorporating systems like SCADA, PLCs, and IoT-enabled devices, organizations can achieve real-time monitoring, improved process control, and predictive maintenance.
Automation reduces the need for human intervention in hazardous conditions, enhancing safety while lowering operational costs and minimizing downtime. From upstream exploration to downstream refining, automation optimizes workflows, increases efficiency, and ensures consistent product quality, enabling the industry to meet rising energy demands with greater reliability and sustainability.
OPERATIONS AND SPECIALIZED SERVICES
UPSTREAM OIL AND GAS
Upstream oil and gas operations focus on exploration, drilling, and production of crude oil and natural gas. These processes are often complex, data-intensive, and operate in challenging environments where efficiency, safety, and reliability are paramount. We offer cutting-edge solutions tailored to meet these demands, including real-time monitoring systems, digital twin technology, and advanced process control.
By integrating automation technologies like SCADA, IoT-enabled devices, and predictive analytics, Jiyu Automation enhances asset management, improves decision-making, and minimizes downtime. These solutions empower upstream operators to optimize performance, reduce costs, and ensure sustainable and reliable energy production.
MIDSTREAM OIL & GAS
Midstream oil and gas operations emphasize on the transportation, storage, and distribution of crude oil, natural gas, and refined products. These processes require seamless integration, precise control, and robust safety measures to ensure efficiency and reliability. Our expert team provides advanced solutions tailored to the midstream sector, including real-time monitoring systems, pipeline automation, and digital twin technology.
By utilizing SCADA, IoT-enabled devices, and predictive analytics, Jiyu Automation optimizes pipeline operations, enhances asset integrity management, and minimizes downtime. These innovative technologies enable midstream operators to improve performance, reduce operational risks, and ensure the safe and efficient movement of energy resources.
DOWNSTREAM OIL & GAS
Downstream refers to the filtering of the raw materials obtained during the upstream phase. This means refining crude oil and purifying natural gas. The marketing and commercial distribution of these products to consumers and end users in a number of forms including natural gas, diesel oil, petrol, gasoline, lubricants, kerosene, jet fuel, asphalt, heating oil, LPG (liquefied petroleum gas) as well as a number of other types of petrochemicals. We deliver tailored solutions for the downstream sector, including advanced process control, digital twin technology, and real-time monitoring systems.
By integrating SCADA, IoT-enabled devices, and predictive analytics, Jiyu Automation enhances refinery operations, optimizes production processes, and ensures quality control. These cutting-edge technologies empower downstream operators to improve performance, minimize costs, and meet market demands while adhering to safety and environmental regulations.
- Digitalizing Plants with Industrial Automation
Drilling analysis, situational awareness, predictive maintenance, production optimization, turnarounds, cumulative work/SIMOPS, technical surveillance, planning and scheduling, performance monitoring, remote operations, and plant optimization.
Process stabilization, energy consumption tracking, carbon footprint reporting, GHG emissions monitoring, leak detection, and route optimization.
Logic testing, pre-start-up verification, operator and technical personnel training, engineering studies, process simulations, and testing of start-up, stop, and emergency stop sequences.
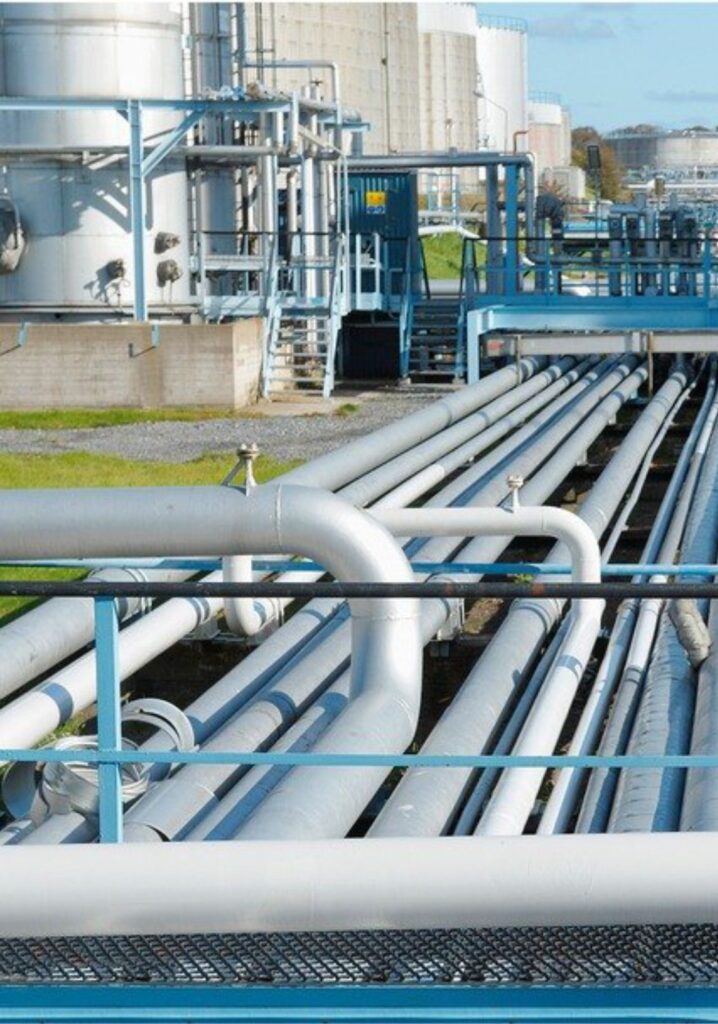
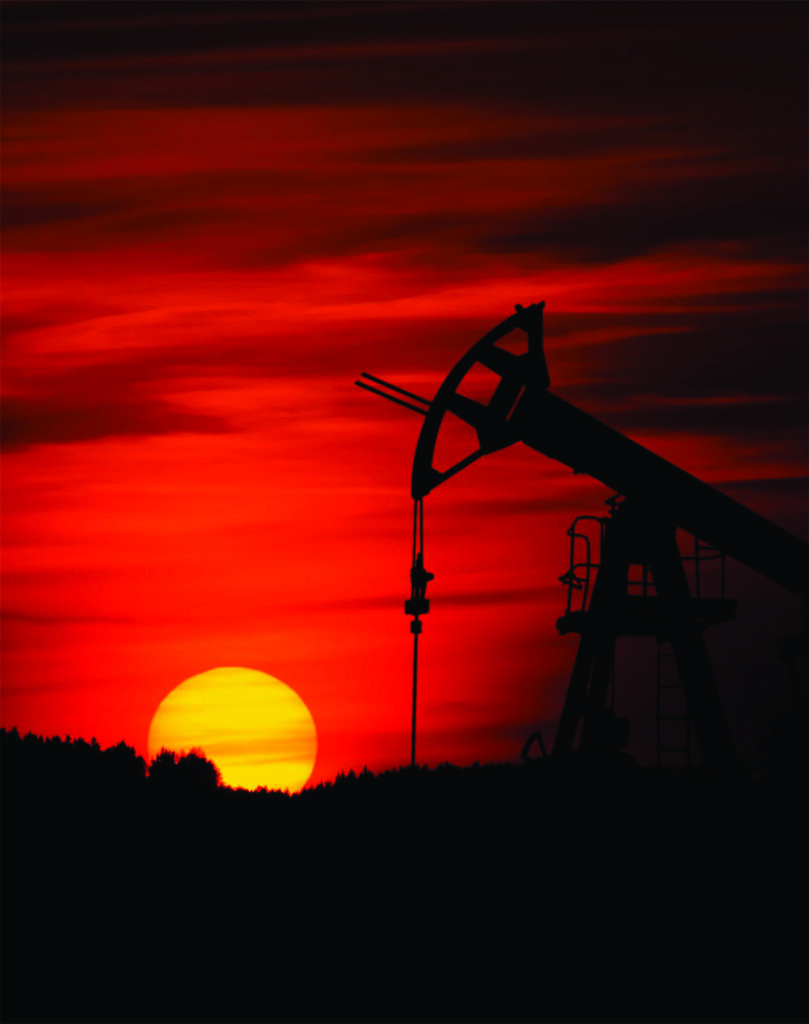
- Research and Innovation Center
OUR TEAM HAS DEVELOPED THE CORE TECHNOLOGIES OF THE SYSTEM, WHICH HAVE BEEN GRANTED 50 CHINESE INVENTION PATENTS, 1 U.S. PATENT, AND 3 AUSTRALIAN PATENTS. THE RESEARCH OUTCOMES HAVE BEEN FEATURED IN PRESTIGIOUS JOURNALS, INCLUDING IEEE TRANSACTIONS ON NEURAL NETWORKS AND LEARNING SYSTEMS, IEEE TRANSACTIONS ON SYSTEMS, MAN, AND CYBERNETICS: SYSTEMS, RELIABILITY ENGINEERING & SYSTEM SAFETY, EXPERT SYSTEMS WITH APPLICATIONS, OCEAN ENGINEERING, INTERNATIONAL JOURNAL OF CONTROL, AUTOMATION AND SYSTEMS, AND OTHERS.
ADVANCED FAULT DIAGNOSIS TECHNOLOGY
We developed a fault re-prediction model for subsea equipment using the Wiener process and dynamic Bayesian networks. Powered by the expectation maximization algorithm, the model achieves high accuracy, with predicted RUL deviating less than 3.5% from actual values. It successfully forecasted failures in the subsea BOP stack and control system, proving its effectiveness in predictive maintenance. This approach enhances reliability and minimizes downtime in subsea operations.

OPTIMIZING OFFSHORE WELL CONTROL
We propose a tenacity-centered, condition-based maintenance strategy for offshore oil well control equipment to reduce costs and operational risks. By optimizing availability and RUL, this approach minimizes downtime and extends equipment life. Implementation has led to a 27% reduction in maintenance costs and a 25% increase in equipment availability, even under harsh conditions. This strategy enhances reliability, efficiency, and sustainability in subsea operations.
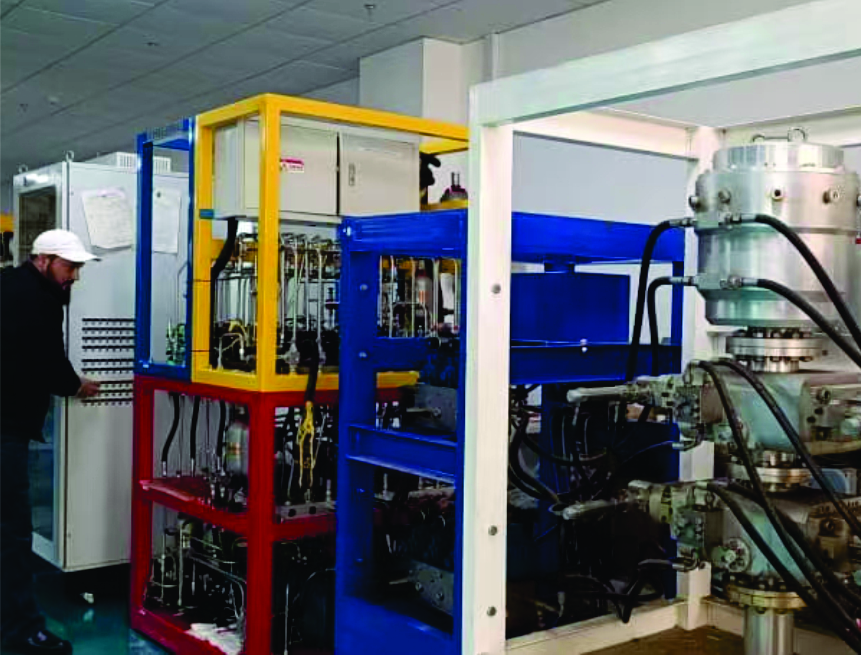
OFFSHORE SAFETY AND EMERGENCY RESPONSE
We have conducted extensive debugging and testing to ensure a reliable system, which has been successfully deployed on key offshore platforms, including South China Sea No. 10 and No. 8, and the Endeavour drilling platform. Notably, it has been applied to China’s first subsea emergency well packer, a major offshore safety milestone. Featured on CCTV, the system enhances the safety, reliability, and efficiency of offshore oil and gas operations, serving as a critical safeguard.
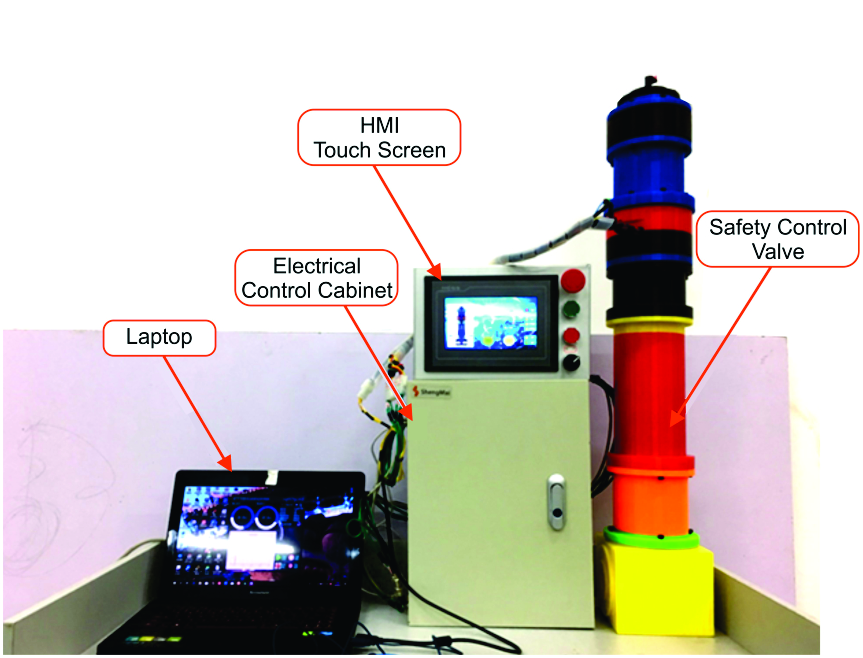