A Digital Twin is an advanced virtual model that replicates the behavior, functionality, and performance of a physical system. It integrates IoT, AI, machine learning, and real-time analytics to create a dynamic and interactive digital representation. This enables organizations to monitor, simulate, and optimize processes without disrupting actual operations.
Digital Twins are widely used across industries such as automotive, manufacturing, oil & gas, and process automation, where real-time monitoring and predictive analytics play a crucial role in ensuring efficiency and sustainability.
In the era of Industry 4.0, Digital Twin Development has emerged as a transformative technology enabling real-time virtual simulation, smart control, and data-driven decision-making. A Digital Twin is a digital replica of a physical system, process, or asset that continuously receives real-time data from sensors and IoT-enabled devices. By mirroring real-world operations in a virtual environment, businesses can optimize performance, predict failures, and improve efficiency. Jiyu Automation, a leader in industrial automation solutions, leverages Digital Twin technology to enhance productivity, reduce operational risks, and drive smarter decision-making in various industries.
APPLICATIONS OF DIGITAL TWIN IN INDUSTRIAL AUTOMATION
Predictive Maintenance
By utilizing real-time data, a Digital Twin can predict potential failures before they occur, reducing downtime, maintenance costs, and unplanned outages. This is crucial in industries such as automotive manufacturing and oil & gas, where equipment reliability directly impacts productivity.
Process Optimization
With a Digital Twin, businesses can run simulations to determine the best operational strategies, ensuring higher efficiency, reduced waste, and improved resource allocation. Manufacturing plants can fine-tune assembly lines, while oil refineries can optimize fuel processing.
Smart Control & Automation
Digital Twins enable intelligent decision-making by analyzing real-time sensor data and suggesting process improvements. Smart control mechanisms ensure that automated systems perform at their peak efficiency, reducing energy consumption and maximizing output.
Supply Chain and Logistics Management
By integrating Digital Twins with supply chain management, businesses can gain real-time visibility into logistics, demand forecasting, and inventory control. This allows companies to respond proactively to disruptions, ensuring smooth operations.
Virtual Testing and Commissioning
Industries can test new automation systems and workflows virtually before implementing them in a live environment. This minimizes risks associated with system failures and ensures seamless deployment of automation technologies.
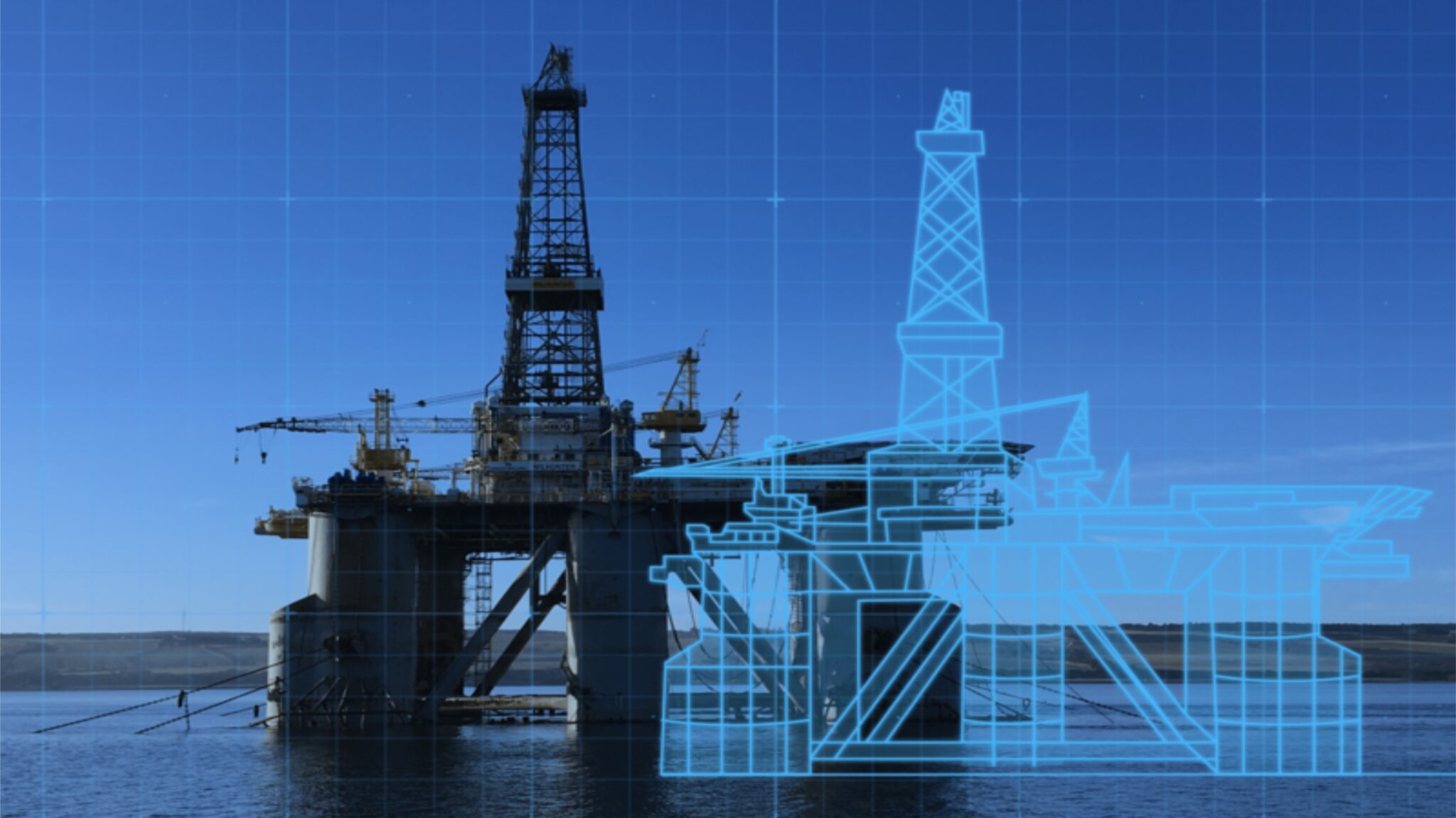
BENEFITS OF DIGITAL TWIN TECHNOLOGY
By simulating real-world scenarios, businesses can optimize processes, reduce energy consumption, and improve resource utilization. Real-time monitoring ensures that inefficiencies are quickly identified and rectified. Predictive analytics allows industries to perform condition-based maintenance, preventing unexpected equipment failures and minimizing costly downtimes. With real-time data insights, Digital Twins empower businesses to make informed and data-driven decisions, leading to enhanced productivity and profitability. As industries evolve, Digital Twins can be adapted and scaled to accommodate new technologies, processes, and business needs, ensuring future-proof automation strategies. By identifying potential failures and operational risks before they occur, businesses can enhance workplace safety and comply with regulatory standards more effectively.
"For over 8 years, Jiyu Automation has been a leader in industrial automation, driving innovation across the automobile, process, and oil & gas industries. Today, we remain committed to advancing automation solutions that enhance efficiency, precision, and sustainability. Together, we shape the future of smart manufacturing."
BEST PRACTICES FOR SUCCESSFUL DIGITAL TWIN IMPLEMENTATION
For successful Digital Twin implementation, businesses must first define clear objectives by identifying specific goals, such as predictive maintenance, process optimization, or energy efficiency. Ensuring data quality and accuracy is essential, as reliable data collection forms the foundation of an accurate and effective digital representation. Investing in scalable infrastructure, including cloud-based and edge computing solutions, helps manage and process large volumes of real-time data efficiently. Additionally, seamless integration with existing automation systems ensures interoperability and maximizes efficiency. Continuous monitoring and regular updates of Digital Twin models with real-time data keep them relevant and effective, allowing businesses to optimize operations and drive smarter decision-making.
As industries continue to embrace Industry 4.0, the role of Digital Twins will expand further with advancements such as AI-driven autonomous systems that enable self-optimizing automation and decision-making. The implementation of 5G connectivity will enhance real-time simulation capabilities by enabling faster data transmission, improving the responsiveness and accuracy of Digital Twin models. Augmented Reality (AR) and Virtual Reality (VR) integration will allow engineers and operators to interact with Digital Twins more intuitively, improving visualization and control. Additionally, blockchain technology will play a crucial role in securing data exchange, ensuring transparency, and protecting sensitive industrial information from cyber threats.