A machine vision system is essentially a technology that enables machines to “see” and interpret images. This system typically consists of cameras or sensors, lighting, and vision software that work together to analyze images and data. It’s commonly used in manufacturing and industrial applications for tasks like inspection, quality control, sorting, and assembly. In an industrial setting, machine vision is often paired with automation systems like robots or conveyors. The system provides real-time feedback and enables processes to be adjusted instantaneously for higher efficiency. It helps in identifying defects, ensuring correct assembly, and making sure the end product meets specifications.
Machine vision systems play a crucial role in the modern industrial landscape, contributing to enhanced automation, quality control, and precision. Whether applied in assembly lines, inspection processes, or robotics, these systems are designed to improve accuracy and operational efficiency. Machine vision systems are equipped with cameras, lighting, and processing units to capture and analyze visual data, helping industries achieve a level of automation that ensures minimal human intervention while maintaining the highest possible quality standards.
The installation of a precise machine vision system is a sophisticated process that requires careful planning, selection of appropriate components, integration into existing workflows, and fine-tuning. Successful installation can significantly improve product quality, reduce downtime, and optimize overall productivity.
THE IMPORTANCE OF PRECISE MACHINE VISION SYSTEMS
The precision of a machine vision system is directly tied to its ability to deliver high-quality outcomes. In industries like automotive, pharmaceuticals, and electronics, even the slightest error can lead to defects, wastage, or even machine failure. Machine vision systems have revolutionized these industries by enabling highly accurate and efficient monitoring and control.
Accuracy: A precise machine vision system ensures that measurements and inspections are conducted with a high degree of precision. This reduces the possibility of errors that might occur with manual inspection or traditional methods.
Efficiency: By automating inspection and measurement tasks, machine vision systems reduce the need for human intervention. This leads to faster processing times and fewer mistakes. Additionally, these systems are capable of running 24/7 without breaks, which maximizes productivity and minimizes downtime.
Cost-Effectiveness: With fewer errors and a reduction in the need for manual labor, machine vision systems offer a cost-effective solution in the long run. They minimize the risk of defective products and waste, leading to improved profitability.
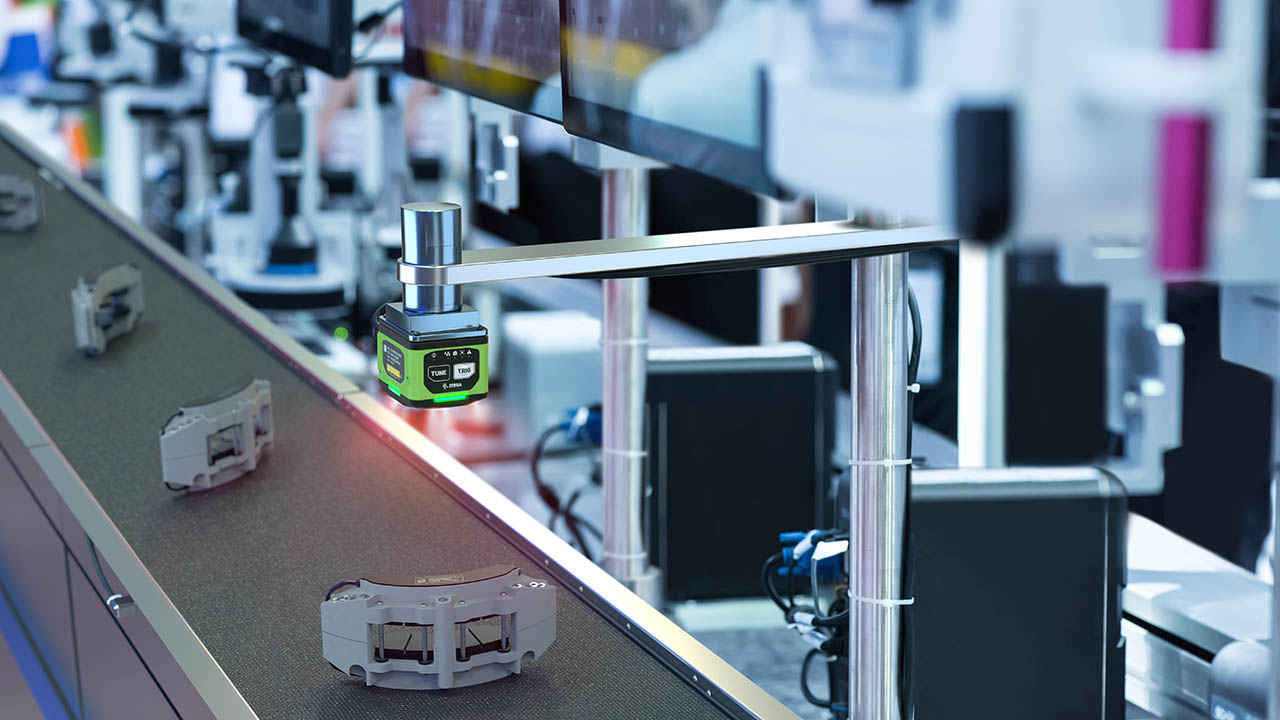
KEY COMPONENTS OF A MACHINE VISION SYSTEM
To achieve precise results, every component of the machine vision system needs to be carefully selected and calibrated. Here are the main components involved in its setup:
Cameras/Sensors: The heart of a machine vision system, cameras are responsible for capturing images or videos. Cameras can be either analog or digital, and their choice depends on the specific application and the environment. High-resolution cameras are often used in tasks where fine details need to be captured, such as inspecting printed circuit boards (PCBs) or assembly components in automotive manufacturing.
Lighting: Proper lighting is critical to machine vision performance. Lighting must be uniform and sufficient to illuminate the object being inspected without creating shadows or reflections. Different types of lighting (LED, fluorescent, or halogen) can be used depending on the type of product and the environment. The angle, intensity, and color of lighting also affect the quality of the images captured.
Processing Unit: Once the images are captured, they need to be processed. The processing unit typically includes a computer or embedded system with the required vision software to analyze the data. This unit evaluates the images for defects, dimensions, or other specifications and provides the output for decision-making.
Software: The software plays a crucial role in analyzing the images. It can be custom-built or off-the-shelf, depending on the specific needs of the installation. The software’s algorithms allow the system to identify patterns, edges, and other visual cues to make measurements, detect defects, and control actions.
Mounting Equipment: Cameras and sensors need to be mounted securely in the correct position for optimal image capture. Adjustable mounts, rails, or holders are used to precisely position the equipment at the correct angle, height, and distance for the task at hand.
Connectivity: Machine vision systems are often part of a larger industrial automation system. As such, they must be integrated with other machines and control systems, such as robots or conveyors. The connectivity between these systems is vital for seamless data exchange and real-time decision-making.
"For over 8 years, Jiyu Automation has been a leader in industrial automation, driving innovation across the automobile, process, and oil & gas industries. Today, we remain committed to advancing automation solutions that enhance efficiency, precision, and sustainability. Together, we shape the future of smart manufacturing."
BENEFITS OF PRECISE MACHINE VISION SYSTEM INSTALLATION
A precise machine vision system, when properly installed and optimized, provides numerous benefits to manufacturing operations. By detecting defects early and ensuring adherence to specifications, it enhances product quality while minimizing costly recalls or returns. Automation accelerates the inspection process, boosting production rates without sacrificing accuracy. Additionally, machine vision systems reduce operational costs by lowering defect rates, minimizing rework, and decreasing reliance on manual labor. As production demands evolve, these systems offer scalability, allowing businesses to expand capacity or handle more complex tasks without major modifications. Furthermore, real-time monitoring and feedback enable immediate process adjustments, preventing defects and optimizing overall efficiency.