The integration of Robots and Automated Guided Vehicles (AGVs) is transforming industrial automation, offering unparalleled efficiency, flexibility, and scalability. Modern manufacturing and logistics operations are increasingly leveraging these technologies to streamline processes, optimize workflows, and enhance productivity. The synergy between robots and AGVs allows for seamless material handling, precise automation, and reduced operational costs. As industries move towards Industry 4.0, the demand for integrated automation solutions continues to grow, ensuring smart, flexible, and responsive operations.
Industrial robots are programmable machines designed to perform repetitive tasks with high precision and consistency. These robots can be classified into different types, including articulated robots, SCARA robots, cartesian robots, and collaborative robots (cobots). Each type serves specific purposes such as welding, painting, pick-and-place operations, and working alongside human operators safely.
Automated Guided Vehicles (AGVs) are self-guided mobile robots used for material transportation in warehouses, factories, and distribution centers. They navigate using predefined paths marked by magnetic strips, laser guidance, or GPS-based tracking. The different types of AGVs include towing AGVs for pulling carts, unit load AGVs for carrying pallets, forklift AGVs for stacking goods, and hybrid AGVs that can operate both autonomously and manually.
THE IMPORTANCE OF INTEGRATING ROBOTS AND AGVS
The integration of robots and AGVs creates a cohesive automation ecosystem, enhancing manufacturing, warehousing, and logistics operations. The combined power of stationary robotic arms and mobile AGVs enables seamless material transport and processing, increased operational efficiency and accuracy, reduction in human errors and labor costs, improved workplace safety and compliance, and scalability for future expansions.
In manufacturing and assembly lines, robotic arms handle tasks like welding, painting, and part assembly, while AGVs transport components between workstations, ensuring continuous production flow. In warehousing and logistics, AGVs automate material movement, retrieving and delivering goods to robotic workstations for sorting, packing, or inspection, which improves inventory management and order fulfillment.
The automotive industry extensively uses robots for assembling vehicle components, with AGVs autonomously transporting parts between robotic work cells. In pharmaceutical and healthcare industries, robots perform precise filling, packaging, and labeling, while AGVs ensure secure transport of sensitive materials. Hospitals also use AGVs for medication and supply delivery, reducing workload for medical staff. Similarly, in the food and beverage industry, robots and AGVs help in food processing, packaging, and logistics by automating material handling, reducing contamination risks, and maintaining quality standards.
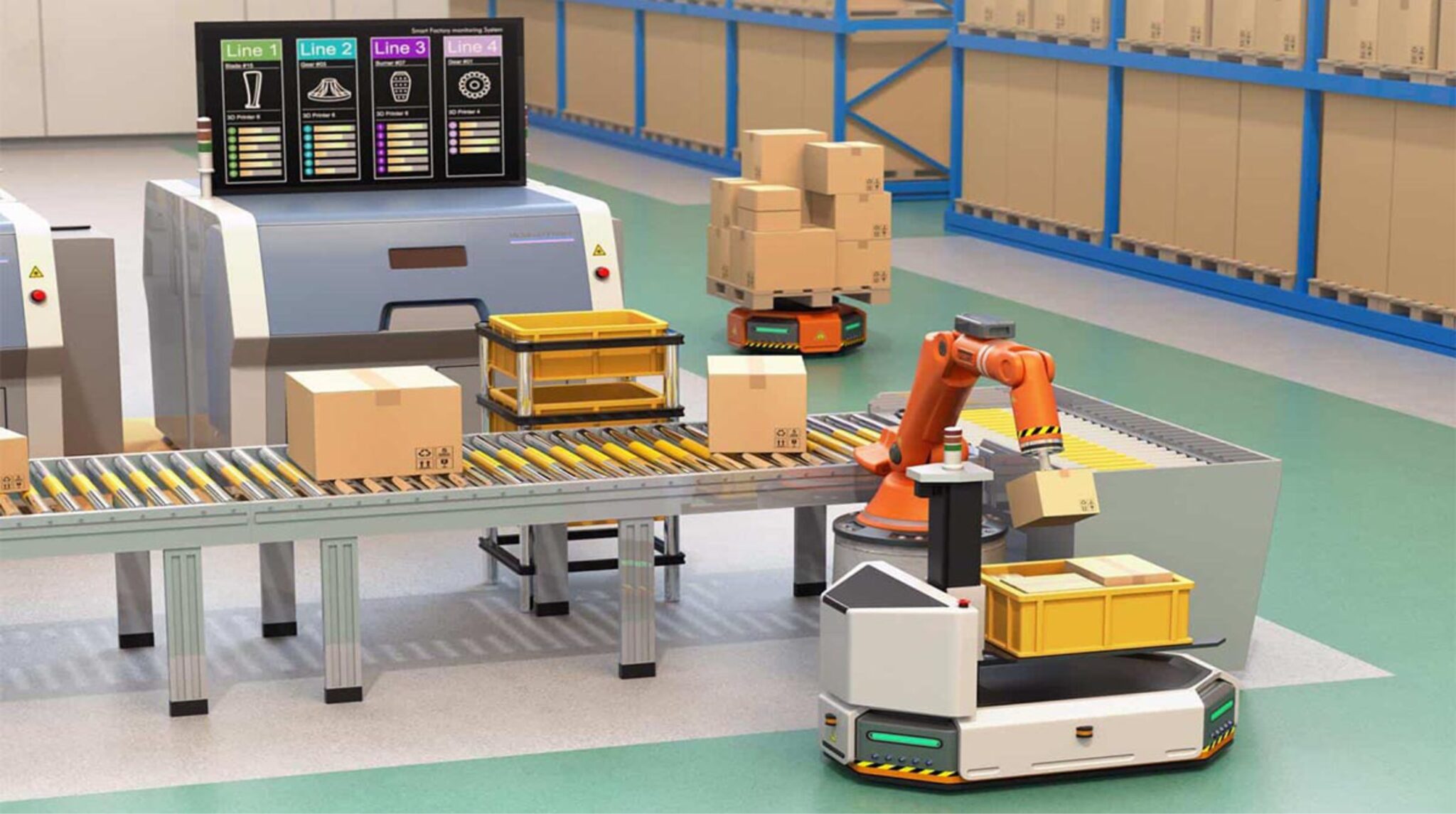
KEY TECHNOLOGIES ENABLING INTEGRATION
The Internet of Things and Industry 4.0 connectivity enable seamless communication between robots, AGVs, and control systems. Sensors and real-time data exchange enhance coordination, allowing predictive maintenance and workflow optimization. AI and Machine Learning improve decision-making, optimize routes, and enhance task execution efficiency, while advanced navigation and vision systems such as LiDAR, GPS, and 3D vision enhance autonomous movement and precision handling.
Collaborative robotics and human-machine interaction ensure that cobots and AGVs work safely alongside human operators. These technologies incorporate safety mechanisms such as sensors and intelligent obstacle avoidance to prevent accidents and promote smooth collaboration.
The integration of robots and AGVs increases productivity and efficiency by automating material handling and processing tasks, reducing operational bottlenecks. It enhances flexibility and scalability, allowing easy reprogramming and reconfiguration for different tasks. Workplace safety improves, as automation reduces exposure to hazardous environments, and compliance with safety regulations is enhanced. Additionally, cost savings are realized through reduced labor expenses, minimized errors, and optimized resource utilization, leading to substantial long-term savings. Real-time data insights and predictive maintenance ensure continuous system monitoring, reducing downtime and improving overall efficiency.
"For over 8 years, Jiyu Automation has been a leader in industrial automation, driving innovation across the automobile, process, and oil & gas industries. Today, we remain committed to advancing automation solutions that enhance efficiency, precision, and sustainability. Together, we shape the future of smart manufacturing."
CHALLENGES AND FUTURE TRENDS
Despite these advantages, some challenges must be addressed for successful integration. High initial investment costs require careful budget planning, and ensuring system compatibility and interoperability demands robust software solutions. Maintenance and technical expertise are crucial for troubleshooting automation systems efficiently, and cybersecurity risks must be managed to protect data and operations from cyber threats.
For a successful integration, businesses should conduct a thorough feasibility study to assess operational needs and workflow requirements. Selecting the right technologies that align with production processes and future scalability is crucial. Ensuring seamless software integration for real-time monitoring and control improves system efficiency. Training the workforce for effective collaboration with automation technology enhances productivity. Implementing regular maintenance and upgrades ensures optimal system performance and longevity.
The future of industrial automation is shaping up with groundbreaking advancements, including 5G connectivity for faster data exchange, AI-driven predictive maintenance, hyper-automation and digital twins for process simulation, and edge computing to enhance real-time decision-making in robotic operations.